Dubai CommerCity (DCC), the region’s first dedicated e-commerce free zone
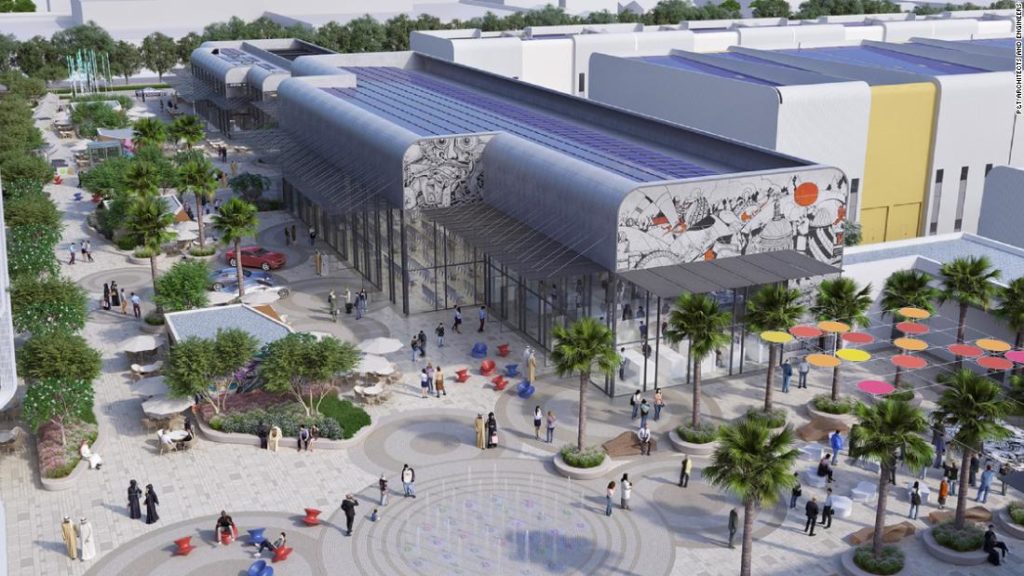
Middle East’s e-commerce market is set to reach around $69 billion by 2020, becoming one of the world’s fastest growing international markets. DCC will play a pivotal role in the development of the e-commerce sector. It will provide growth opportunities for global and regional manufacturers, as well as distributors and global e-retailers. DCC will offer a unique e-commerce ecosystem for companies in the industry such as software as a service, logistics as a service, call centers, web developers, photoshoot studios amongst others.
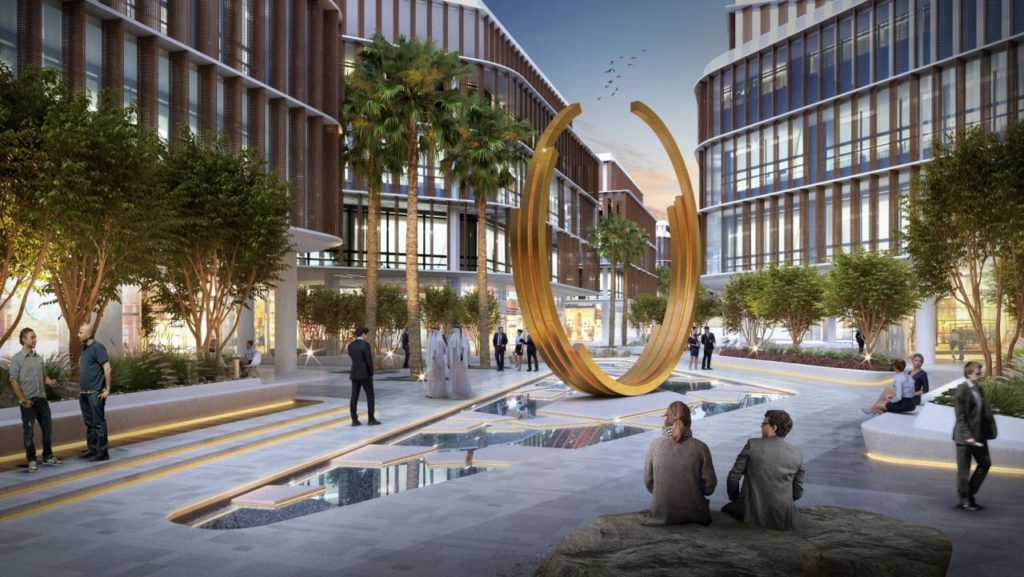
Dubai CommerCity is the first e-commerce free zone dedicated to the growing E-commerce market in the Middle East, North Africa and South Asia (MENASA) region. It is a joint venture between Dubai Airport Freezone Authority (DAFZA) and Wasl Asset Management Group with an investment of AED 3.2 billion spread over an area of approximately 2.1 million square feet. The free zone is a strategic project, aimed at elevating Dubai’s position as a leading center for e-commerce. It is set to shape the future of e-commerce in Dubai, becoming a regional hub for the industry by providing unique services that add value to customers’ businesses.
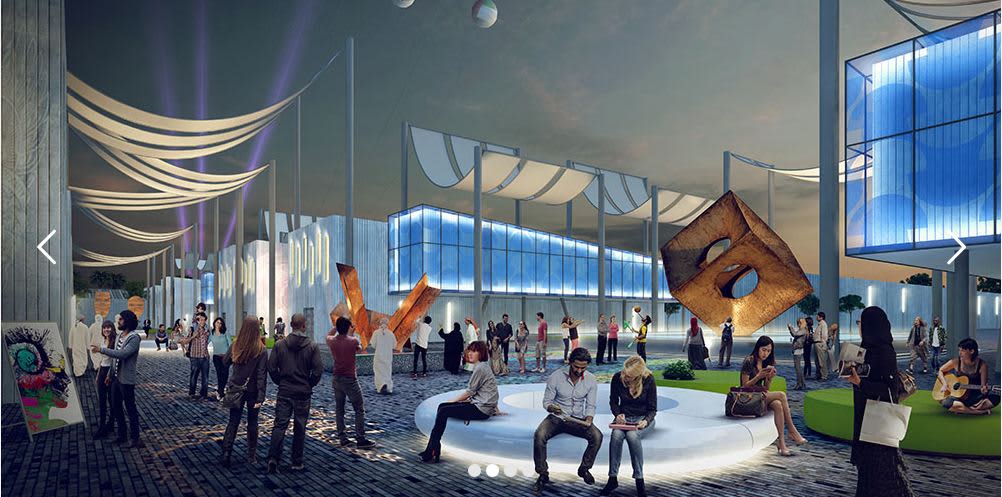
Dubai CommerCity is spread across a total built up area of 520,000 SQM with office spaces of 240,000 SQM and logistics units covering 54,000 SQM. Dubai CommerCity is divided into three modern and innovatively-designed clusters: the Business Cluster containing 12 modern g +6 office buildings and green spaces; the Logistic Cluster consisting of 105 logistic units (dedicated and multi-client) equipped with the latest technology; and the Social Cluster comprising of multi-purpose halls, flagship and super stores where customers can exhibit their products, science labs to innovate, photoshoot studios, modular exhibition centers, wellness centers and a range of restaurants and cafés. Dubai CommerCity has implemented state-of-the-art technologies to provide investors with a smart & quality-focused business ecosystem. First batch of Phase-I will be delivered in Q4 2020.